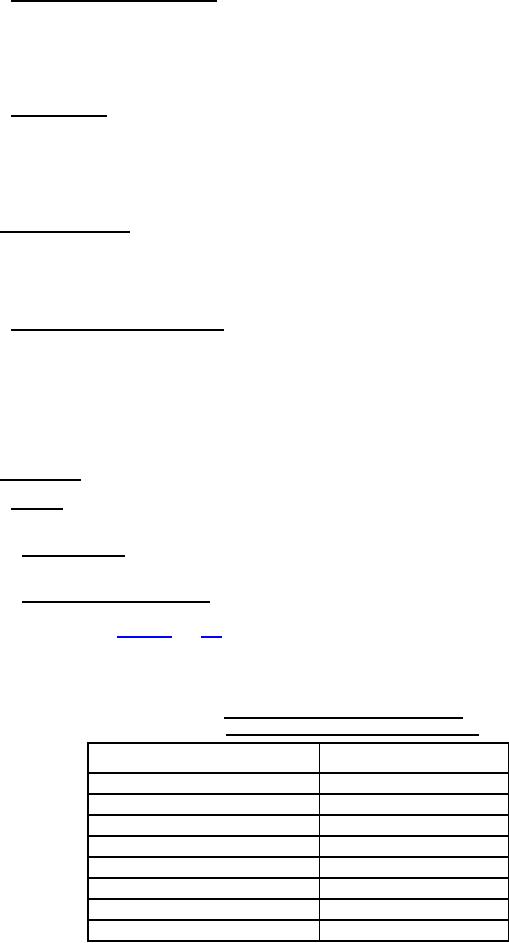
MIL-PRF-24635E
4.3.2 Sampling for conformance testing. The contractor shall select a production sample sufficiently large
enough to permit the performance of all conformance tests. If it is required, two representative packaged samples
(four samples for plural component systems) shall be forwarded to a designated laboratory for verification tests. If
sample panels are to be coated at the vendor's facility and forwarded to an external laboratory for testing,
preparation of the panels and application of the coating system must be observed by a representative from the
Defense Contracts Management Agency (DCMA).
4.3.3 Noncompliance. If a sample fails to pass its conformance inspections, the lot shall be rejected and the
manufacturer shall notify the cognizant inspection activity of such failure and take corrective action on the materials
or processes, or both, as warranted. Acceptance and shipment of the product shall be discontinued until corrective
action, suitable to the inspection activity, has been taken. After the corrective action has been taken, conformance
inspections shall be repeated on the new lot. In the event of failure after re-inspection, information concerning the
failure shall be furnished to the cognizant inspection activity.
4.4 Inspection conditions. Unless otherwise specified, all inspections shall be performed in accordance with
the test conditions specified in the routine and referee testing conditions of FED-STD-141. The term referee
conditions shall mean a temperature of 73±2 °F (23±1 °C) and a relative humidity of 50±4 percent. Unless
otherwise specified, all paint test specimens shall be cured to service in accordance with manufacturer's
ASTM F718 sheet before testing.
4.4.1 Test panels and surface preparation. Unless otherwise specified, test panels shall be nominal 150 by 300
by 3 mm (6 by 12 by 0.125 inch) plate aluminum or cold rolled steel. Test panels shall be degreased in accordance
with Methods B, C, or D of ASTM D609. The degreased test panels shall be abrasive blasted with new, clean
aluminum oxide to provide an average profile pattern of 0.051 to 0.076 mm (0.002 to 0.003 inch) on both sides. For
direct-to-metal coating systems, the panels shall remain unprimed prior to application of the coating system. For
coatings requiring an anti-corrosive primer, the panels shall be primed with the primer included by the manufacturer
as part of the coating system, or with a primer in accordance with MIL-DTL-24441 if no primer component is
identified by the manufacturer for the coating system.
4.5 Test methods.
4.5.1 Toxicity. To determine conformance with the requirements of 3.4, the material shall be evaluated by the
4.5.1.1 Asbestos content. Asbestos content shall be determined on a dry film of the coating in accordance with
29 CFR 1915.1001, Appendix K, and the results shall be recorded as a percent by weight of the dry coating film.
4.5.1.2 Soluble and total metal content. Soluble and total metal content, except tantalum and tungsten, shall be
determined on a dry paint film of the coatings in accordance with the 40 CFR 261, Appendix II, Method 1311, and
the appropriate test listed in tables VI and VII. Soluble metal content shall be reported as milligrams per liter
(mg/L). Total metal content shall be reported as percent by weight of the dry coating film. Tantalum and tungsten
soluble metal content and total metal content shall be analyzed as specified in 4.5.1.2.1.
TABLE VI. Test methods for evaluating solid waste
physical/chemical methods, EPA SW-846.
Metal/material
Digestion test method
All metals, except chromium (VI)
3050
Chromium (VI)
3060
Antimony
7040 or 7041
Arsenic
7060 or 7061
Barium
7080 or 7081
Cadmium
7131
Total chromium
7190
Chromium (VI)
7195, 7196, or 7197
18
For Parts Inquires call Parts Hangar, Inc (727) 493-0744
© Copyright 2015 Integrated Publishing, Inc.
A Service Disabled Veteran Owned Small Business