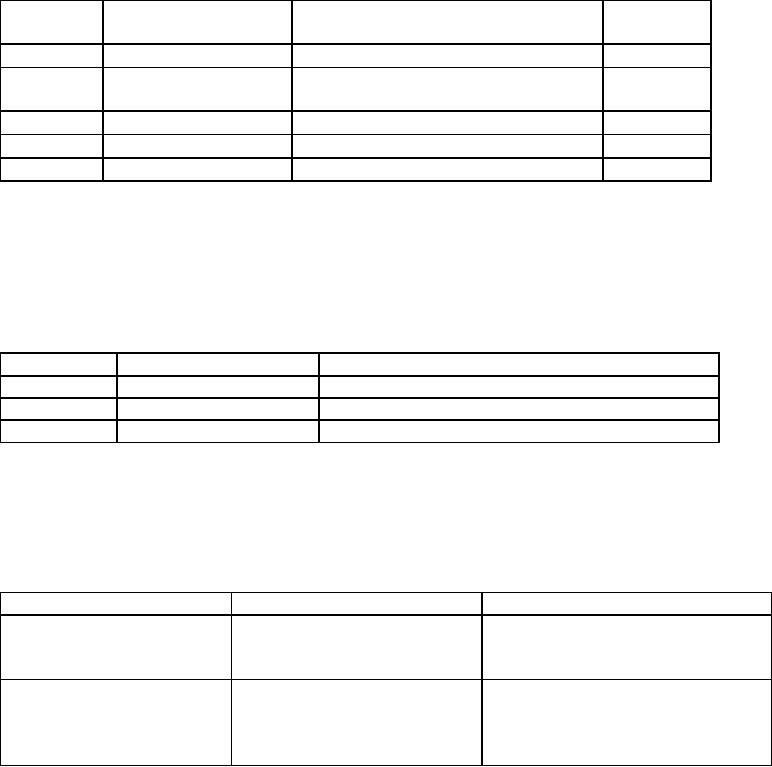
MIL-PRF-83936C(USAF)
or its equivalent in accordance with ASTM D2196. Readings shall be taken after the spindle has
been operating for a minimum of three minutes.
TABLE II
METAL
SPECIFICATION/
SURFACE TREATMENT
WEIGHT
STANDARD
CHANGE
±4.0 mg
Aluminum
ASTM B209 (2024-T3) As Received
Aluminum
ASTM B209 (2024-T3) MIL-A-8625 Type II, Class I
1900 - 2100 mg/sq ft
-4.0 mg
±20.0 mg
Magnesium
SAE AMS 4377
MIL-M-3171, Type III
±4.0 mg
Steel
SAE AMS 5046
As Received
±40.0 mg
Steel
SAE AMS 5046
MIL-STD-870 Type II, Cl I (Cad. Plate)
NOTE: All panels shall be cleaned/degreased with a suitable solvent, oven dried at 375° F for 1 hour,
and desiccated for 1/2 hour prior to surface treatment and/or testing. Panels shall be sheared/cut prior
to surface treatment.
TABLE III
METAL
SPECIFICATION
SURFACE TREATMENT
Aluminum
ASTM B209 (2024-T3)
MIL-A-8625, Type II, Class I, Dichromate Seal
Magnesium
SAE AMS 4377
MIL-M-3171, Type III
Steel
SAE AMS 5046
MIL-STD-870, Type II, Class 1
NOTE: All panels shall be sheared/cut prior to surface treatment. All panels shall be
cleaned/degreased with suitable solvent prior to surface treatment and painting.
TABLE IV
COATING SYSTEM
DRY FILM THICKNESS
DRYING TIME STD CONDITIONS
Wash Primer, MIL-C-8514
0.3 - 0.5 mils
1 hr
Topcoat, MIL-L-81352
2 coats (0.5 - 0.7 mils each)
8 hr
Epoxy Primer, MIL-C-23377
0.5 - 0.9 mils
1 hr
Urethane Topcoat,
2 coats
4 hrs between coats. 48 hrs after last
MIL-C-83286
0.8 - 1.1 mils each
coat
NOTE: After coating systems are applied to both sides of the test panel and cured as above, all
panels shall be baked for 96 hours at 210° ± 10° F cooled to ambient temperature and stored in a
desiccator (or equivalent) until used for test.
6
For Parts Inquires call Parts Hangar, Inc (727) 493-0744
© Copyright 2015 Integrated Publishing, Inc.
A Service Disabled Veteran Owned Small Business