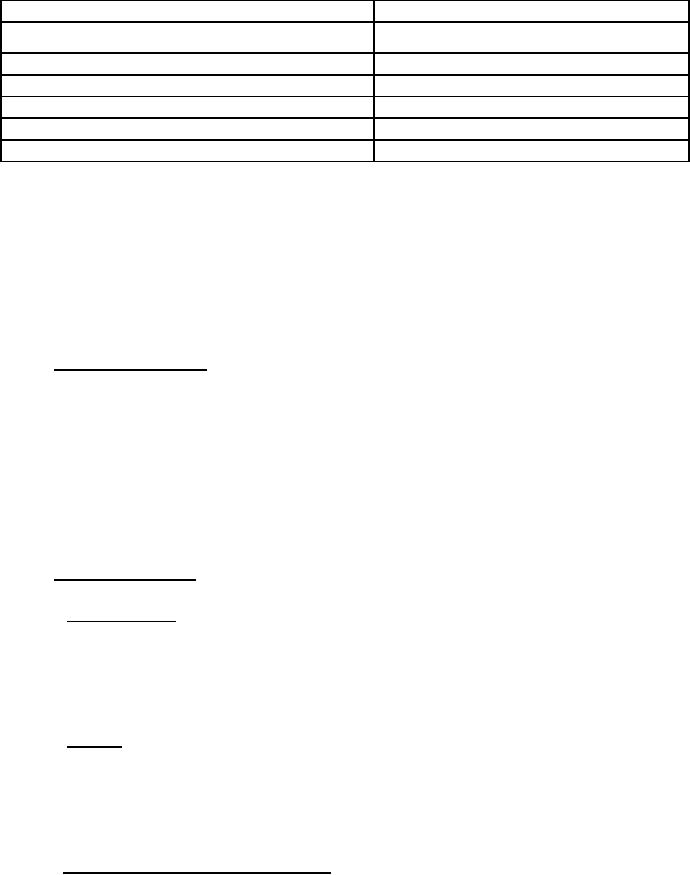
MIL-DTL-12276E(MR)
CHEMICAL and SOLVENTS
IMMERSION TIME
Boiling toluene
1 hour
Glacial acetic acid
1 hour at room temperature
Ammonium hydroxide (10 percent by weight)
1 hour at room temperature
Ethyl alcohol
1 hour at room temperature
Ethyl ether
1 hour at room temperature
Boiling bis-(beta chloroethyl) ether
2 hours (type II varnish only)
Coated panels which are to be immersed in acetic acid and ammonium hydroxide shall
have their edges protected by dipping in molten paraffin prior to immersion. The paraffin
shall not extend more than 1/8 inch onto the coated area of the panels.
At the end of the specified test period, the film of the varnish shall not have soften,
blistered or otherwise deteriorated. (During the immersion in boiling bis-(beta chloroethyl)
ether, moderate discoloration shall not be considered as deterioration.)
4.3.8 Corrosion resistance. Test panels, 3 x 6 x 0.026 inches in sizes, shall be prepared and
coated as specified in 4.3.1. A minimum of two coated panels for each of the three baking
schedules specified in 4.3.1 shall be tested for corrosion resistance by scribing each panel
along the two diagonals for a distance of 5 inches using a razor blade. The scribe marks
shall completely penetrate the varnish film. Expose the panels for 264 hours (11 days) to 5
percent salt spray in accordance with ASTM B117. At the end of the test period, examine
the panels visually for evidence of peeling or undercutting of the coating at the scribe marks
or signs of rusting at points other than within 1/8 inch distance from the scribe marks or
edges of the panels.
4.3.9 Abrasion resistance.
4.3.9.1 Types I and III. A minimum of two panels for each of the three baking schedules
specified in 4.3.1 shall be used. The shape and size of the panels shall be either a disk of 4
inch diameter x 0.026 inch thick, or a square panel 4 x 4 x 0.026 inches. The panels shall be
prepared and coated as specified in 4.3.1. The test shall be conducted in accordance with
ASTM D4060.
4.3.9.2 Type II. A minimum of two panels for each of the three baking schedules specified
in 4.3.1 shall be used. The shape and size of the panels shall be either a disk of 4 inch
diameter x 0.026 inch thick, or a square panel 4 x 4 x 0.026 inches. The panels shall be
prepared and coated as specified in 4.3.1. The test shall be conducted in accordance with
ASTM D968 and 2 kg of sand shall be used.
4.3.10 Impact resistance (For Type III only). Two test panels, 3 x 6 x 0.026 inches in size,
shall be prepared, coated, and baked as specified in and in accordance with 4.3.1. The
coated panels shall be tested for impact resistance with an impact tester device utilizing a
falling weight and die technology which is capable of exerting 30 inch-pounds of impact on
the panel. The coated panel shall be placed (in the device) with the test surface facing
downward or away from the impacting tool. A 30 inch-pound impact shall be made on the
10
For Parts Inquires call Parts Hangar, Inc (727) 493-0744
© Copyright 2015 Integrated Publishing, Inc.
A Service Disabled Veteran Owned Small Business