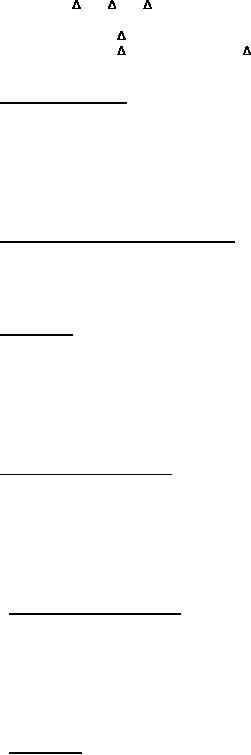
MIL-DTL-24631A(SH)
E, A, B, L in accordance with ASTM D 2244. Determine
change in wetted green reflectance for each test panel.
Average E values. Average wetted green reflectances. The
average E change and RW shall be in accordance with the
requirements of 3.4.3.
4.5.6 Contrast ratio. In accordance with ASTM D 344 paragraphs 6 and 7
using a ratio of 7 milliliters (mL) of paint per 930 square centimeters (cm2)
prepare a smooth surfaced paper chart test having adjacent black and white
color areas and coated with a lacquer or varnish to render the surface
impermeable to the liquid paint. Measure test specimen and calculate contrast
ratio (C) in accordance with ASTM D 2805. Contrast ratio shall be in
accordance with the requirements of 3.4 and the appropriate specification
sheet.
4.5.7 Course particles and skins. Course particles and skins shall be
determined in accordance with method 4092.1 of FED-STD-141 on each individual
component, except that butyl acetate conforming to ASTM D 4615 shall be used
for solvent. Test results shall be in accordance with the requirements of 3.4
and the appropriate specification sheet.
4.5.8 Pot life. One liter (1 quart) of paint shall be prepared in
accordance with 4.4.4, except testing shall begin as soon as mixed. The
consistency shall be determined in accordance with ASTM D 562 at the following
intervals from completion of initial mixing: Once during the first four hours
and every hour for the next four hours. The test shall be terminated when the
consistency exceeds 115 Kreb units, or at the end of eight hours. Pot life
shall be in accordance with the requirements of 3.4.1 and the appropriate
specification sheet.
4.5.9 Brushing properties. The paint shall be prepared as specified in
4.4.4. Without further reduction, the paint shall be applied and laid off in
accordance with method 4321.2 of FED-STD-141 and 4.5 using a natural bristle
brush. After drying for a minimum of 16 hours at ambient laboratory
conditions, the dry paint film shall be observed for: (a) obvious lap marks or
brush marks, (b) gloss and color variations or mottling and (c) pigment
streaking or separation. Test results shall be in accordance with the
requirements of 3.5.1.
4.5.10 Spraying properties. The paint shall be prepared as specified
in 4.4.4. Without further reduction, the paint shall be sprayed on a
sandblasted steel panel to a 4 mil wet film thickness. The steel panel shall
be observed for dusting, floating, mottling, bubbling, wrinkling, streaming,
pinholing, cratering, orange peel, blushing, blooming or silking in accordance
with method 4331.1 of FED-STD-141. The wet and dry sprayed paint films shall
be in accordance with the requirements of 3.5.2. For referee test, use
automatic application in accordance with method 2131 of FED-STD-141.
4.5.11 Adhesion. Prepare neoprene test panel (see 4.4.3) in accordance
with 4.4.3(c) with a spray applied film of the test paint. After curing the
sprayed film for a minimum of 16 hours at ambient laboratory conditions,
immerse the coated neoprene panel in deionized or distilled water for a 24
hour period. After 24 hours in the water, remove the test panel and quickly
pat the surface dry with a paper towel. Within one minute after removal of
the test panel from the water, make two parallel cuts through the coating
surface to or into the neoprene rubber with a sharp knife. The cuts shall be
12
For Parts Inquires call Parts Hangar, Inc (727) 493-0744
© Copyright 2015 Integrated Publishing, Inc.
A Service Disabled Veteran Owned Small Business