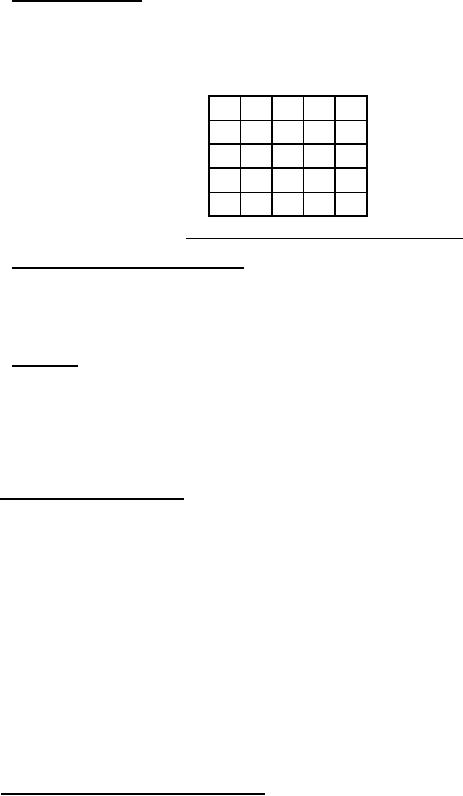
MIL-PRF-24667C
4.5.3.2 Impacting the sample. Immediately upon removal from treatment, each panel shall be subjected to 25
impacts by the tup dropped from a distance of 4.0 feet (1.2 meters). Type IV coatings shall be subject to 3.0 feet
(910 millimeters). The impacts on the panel shall be made in the sequence specified on figure 1. Successive points
of impact shall form a 5 by 5 pattern, enclosed within an area of about 9 square inches (58 square centimeters), in
which the impacts are equally spaced ¾±1/16 inch (20±1.5 millimeters) center-to-center from their nearest neighbors.
2
15
11
7
3
6
19
23
20
16
10
22
25
24
12
14
18
21
17
8
1
5
9
13
4
FIGURE 1. Impact sequence for the impact resistance test.
4.5.3.3 Removal of loosened non-skid coating. Upon completion of each impact test, the panel shall be probed
by hand with a hand held, sharpened, 1 inch (25.4 millimeters) (nominal) steel cold chisel in an area that received no
impacts in order to judge the force needed to remove the coating. The panel shall then be probed in the impact area
with the chisel, using a force less than that used in the non-impact area, and coating which has been loosened by the
impact of the steel ball shall be removed from the panel.
4.5.3.4 Evaluation. The percentage of coating system remaining intact and tightly adhering to the panel shall
be evaluated as follows: In the 5 by 5 pattern of impacts, there are 40 pairs of impacts separated by ¾ inch (20
millimeters) center to center. In every case in which one or more layers of the coating system has been removed
with the chisel, so as to connect one pair of impacts, the percentage of intact coating system is reduced by 2.5. Thus,
a passing value of 90 percent indicates that no more than four pairs of adjacent impacts are connected. Results for
duplicate panels tested under the same conditions shall be averaged. Failure of one of the two conditions constitutes
failure of this test. Impact resistance for each type shall be in accordance with the requirements of 3.6.
4.5.4 Resistance to wear (types I-X). Three steel panels 12 by 6 by inches s (300 by 150 by 3 millimeter)
(nominal) shall be prepared as specified in 4.4.3. The mass of each panel shall be measured to the nearest 0.001
pound (0.5 gram) before application of the coating system. Each panel shall be abraded by the cable abrasion tester
specified in 4.5.2 for 50 cycles and then its mass determined. The panel shall then be worn for an additional 450
cycles in the cable abrasion tester for all Type coatings and an additional 300 cycles for Type V coatings. For
abrasive coatings, the wire in the cable abrasion tester shall be replaced after the first 50 cycles and every 150 cycles
thereafter. After completion of the wear, the final coating mass shall be taken. The percent of determined mass loss
is calculated as follows:
Percent mass loss = 100 x (M2 - M3) / (M2 M1)
M1
Mass of panel before coating
M2
Mass at 50 cycles
M3
Mass at end of test
The average percent of determined mass loss of the three panels shall be computed. Loss of mass shall conform to
the requirements of 3.7.
4.5.5 Protective covering removal (type XI only). Twenty specimens of deck covering, 1 by 7 inches (25 by
178 millimeters), shall be prepared for testing. Ten specimens shall be tested immediately in accordance with
4.5.5.1. Ten specimens shall be placed in an oven at 150±5 °F (68±5 °C) for 7 days cooled for 2 hours, and then
tested in accordance with 4.5.5.1. The amount of effort required to pull protective cover away from adhesive film
shall be determined for each set of ten specimens, the results averaged, and the average of the ten results shall not
exceed the maximum values specified in 3.8.
25
For Parts Inquires call Parts Hangar, Inc (727) 493-0744
© Copyright 2015 Integrated Publishing, Inc.
A Service Disabled Veteran Owned Small Business