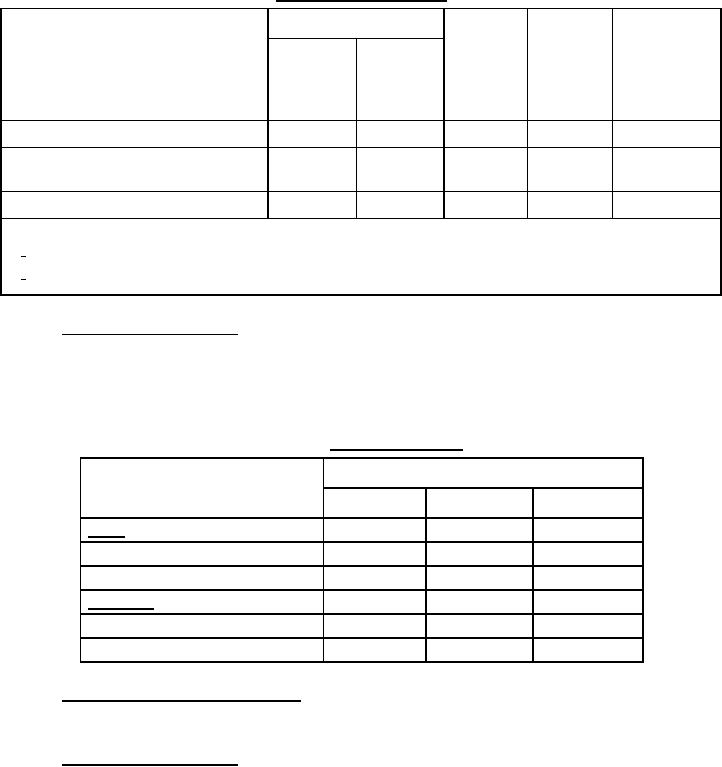
MIL-PRF-24667C
TABLE IV. Identification characteristics - Continued.
Two-part coating
One-part
Type XI
Base
Curing
coating or
Characteristic
Aggregate
sealing
material,
agent,
combined
compound
component
component
mixture
A
B
Flash point
X
X
X
X
Volatile organic content (VOC) (grams
X
X
per liter [g/L] coating less water)
Coverage [ft2/gal (m2/L)]
X
NOTES:
1/
Isocyanate content, ASTM D2572, if applicable.
2/
One-part coating only; these analyses are done on the individual components of two-part coatings.
3.4 Coefficient of friction (COF). The coefficient of static friction of the coating system, when tested in
accordance with 4.5.1, shall be determined on topcoats which have been subjected to 50 cycles of wear (conditioning
of surface) and on topcoats which have completed the wear test as specified in 4.5.4. The test shall be performed on
dry, wet, and oily substrates. When tested in accordance with 4.5.1, the minimum values for each type shall be in
accordance with table V.
TABLE V. Coefficient of friction.
Minimum value
Dry
Wet
Oily
Initial
Types I, V, VI, VII, VIII, and IX
0.95
0.90
0.80
Types II, III, IV, X, and XI
0.90
0.85
0.75
After wear
Types I, V, VI, VII, VIII, and IX
0.90
0.85
0.75
Types II, III, IV, and X
0.85
0.75
0.65
3.5 Abrasion of cable (composition L only). When tested in accordance with 4.5.2, the composition L non-skid
coating system shall produce a maximum average wear of the arresting cable test wire of 0.025 millimeters (1.0 mil;
0.001 inch).
3.6 Impact resistance (types I-X). When tested in accordance with 4.5.3, the minimum impact resistance of
each type of non-skid coating shall be in accordance with table VI. Failure of any one of the four conditions tested
in 4.5.3 to meet the requirements of table VI constitutes failure of this test.
11
For Parts Inquires call Parts Hangar, Inc (727) 493-0744
© Copyright 2015 Integrated Publishing, Inc.
A Service Disabled Veteran Owned Small Business