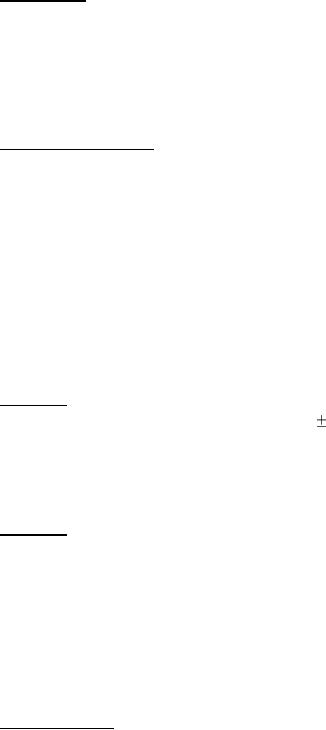
MIL-PRF-25134C(USAF)
4.7.1 Appearance. The remover shall be mixed by brisk hand shaking for a period of 30 seconds
after which it shall be examined for skins, lumps, and homogeneity. Approximately 50 milliliters
of the mixed remover shall then be poured into a 100 milliliter graduated glass cylinder and
allowed to stand for 1 hour. At the end of the 1 hour period, the remover shall be visually
examined for any signs of separation. Any visible separation shall be considered unacceptable and
the material shall be rejected.
4.7.2 Consistency and flow. An enamel-coated aluminum test panel conforming to section 4.6
shall be used for this test. The panel shall be taped as specified in section 4.6 to provide 2.5 by 5-
inch coated areas. A strip of masking tape three quarters of an inch wide shall be placed at the
top of one these areas, and two strips shall be placed at the bottom of the same area. After
taping, the panel shall be placed with its long edge horizontal and its short edge at a 45° angle
from the horizontal. Sufficient well mixed remover shall then be poured along the top edge of the
panel to completely wet and cover the taped-in test area. Application time shall not exceed 10
seconds. The area enclosed by the tape shall be visually examined during the initial run off of
excess remover, then again 5 minutes and 15 minutes after the initial application. The remover
shall drain so that a heavy, wet film remains over the entire test area of the panel. No evidence of
shearing action or dry spotting of the film is acceptable.
4.7.3 Viscosity. A 450-milliliter sample of the remover shall be placed in a 600-milliliter beaker.
Viscosity of the sample shall be determined at 77° 3°F using a Model LVF Brookfield
Viscometer, or its equivalent, with a No. 3 spindle operating at 30 rpm in accordance with ASTM
D2196. Readings shall be taken after the spindle has been operating for a minimum of 3 minutes.
Material shall be rejected if viscosity is less than 6.0 or greater than 14.0 poises.
4.7.4 Volatility. A Petri dish, 9 centimeters in diameter and 1.5 centimeters deep, shall be placed
on each pan of a two-pan beam balance. Sufficient remover shall be added to cover the entire
bottom of one of the dishes. Distilled water shall be carefully poured in the other dish until the
dish containing the remover is counter balanced. The balance with the Petri dishes on the pans
shall be exposed for 30 minutes in a draft-free atmosphere having a temperature of 75°± 5°F and a
relative humidity of 50%± 5%. At the end of the exposure period, the comparative loss in
weights shall be observed. If the paint remover weight loss exceeds weight loss of the distilled
water, the material shall be rejected.
4.7.5 Removal power. Place one of each of the three different test panels prepared as specified in
4.6 in a suitable container with the long edge horizontal and the short edge at a 45° angle to the
horizontal. Pour just enough of the well mixed comparison formula along the top edge of the
panel to completely wet one of the coated test areas, allowing the excess to drain off. Do not
permit application time to exceed 10 seconds. Note the time at which application is started and
the time when lifting or wrinkling of the coating is complete. Within one minute of initial
application, repeat the process on the next panel. Continue with the process to establish optimum
removal time for each type of test panel for the comparison formula. Repeat the above process,
alternating test areas with test remover and comparison formula, and leaving the remover on the
panel for the time established during the first part of the test. When the established optimum time
9
For Parts Inquires call Parts Hangar, Inc (727) 493-0744
© Copyright 2015 Integrated Publishing, Inc.
A Service Disabled Veteran Owned Small Business